The BYO (Boost Your Output) project at the Bibiyana Gas Plant required the installation of two new GE Prolec power transformers to support the increased power demand generated by the introduction of Turbo Expanders and Booster Compressors. This complex process involved managing 22 critical stages, each with its unique challenges. Below is a summary of how these challenges were successfully managed from Stage 1 – Approval on Technical Aspects to Stage 22 – Packing & Delivery.
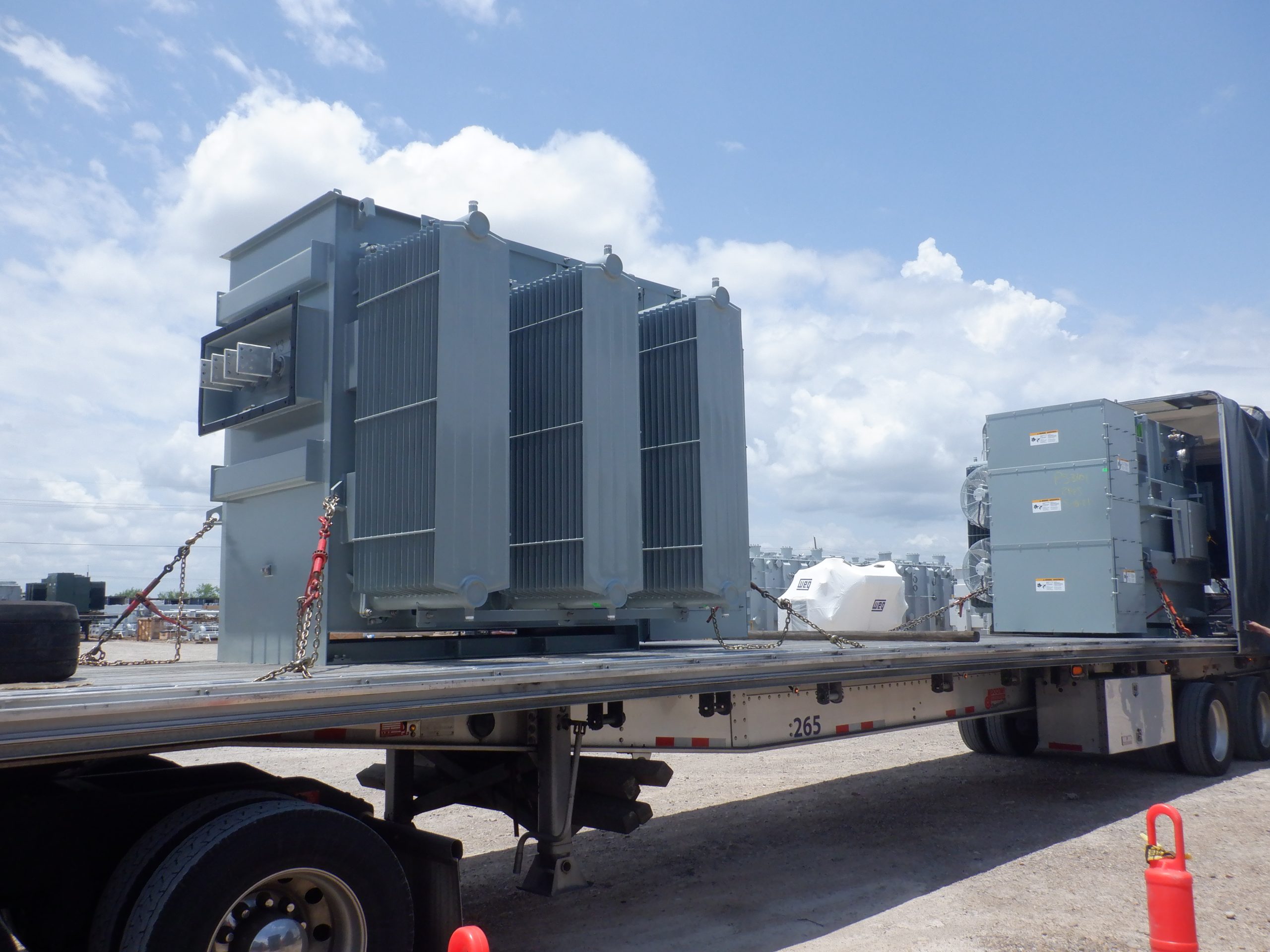
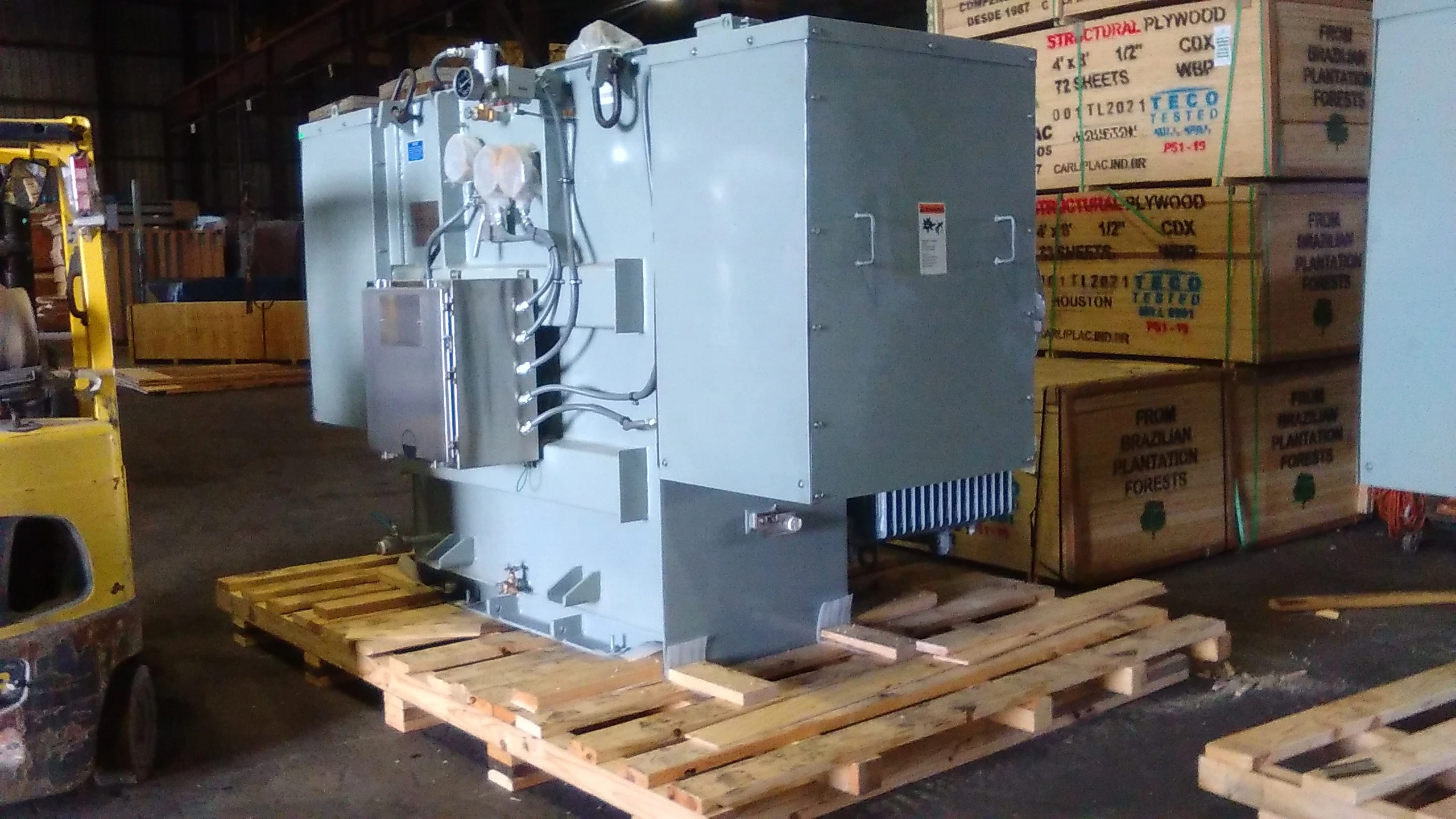
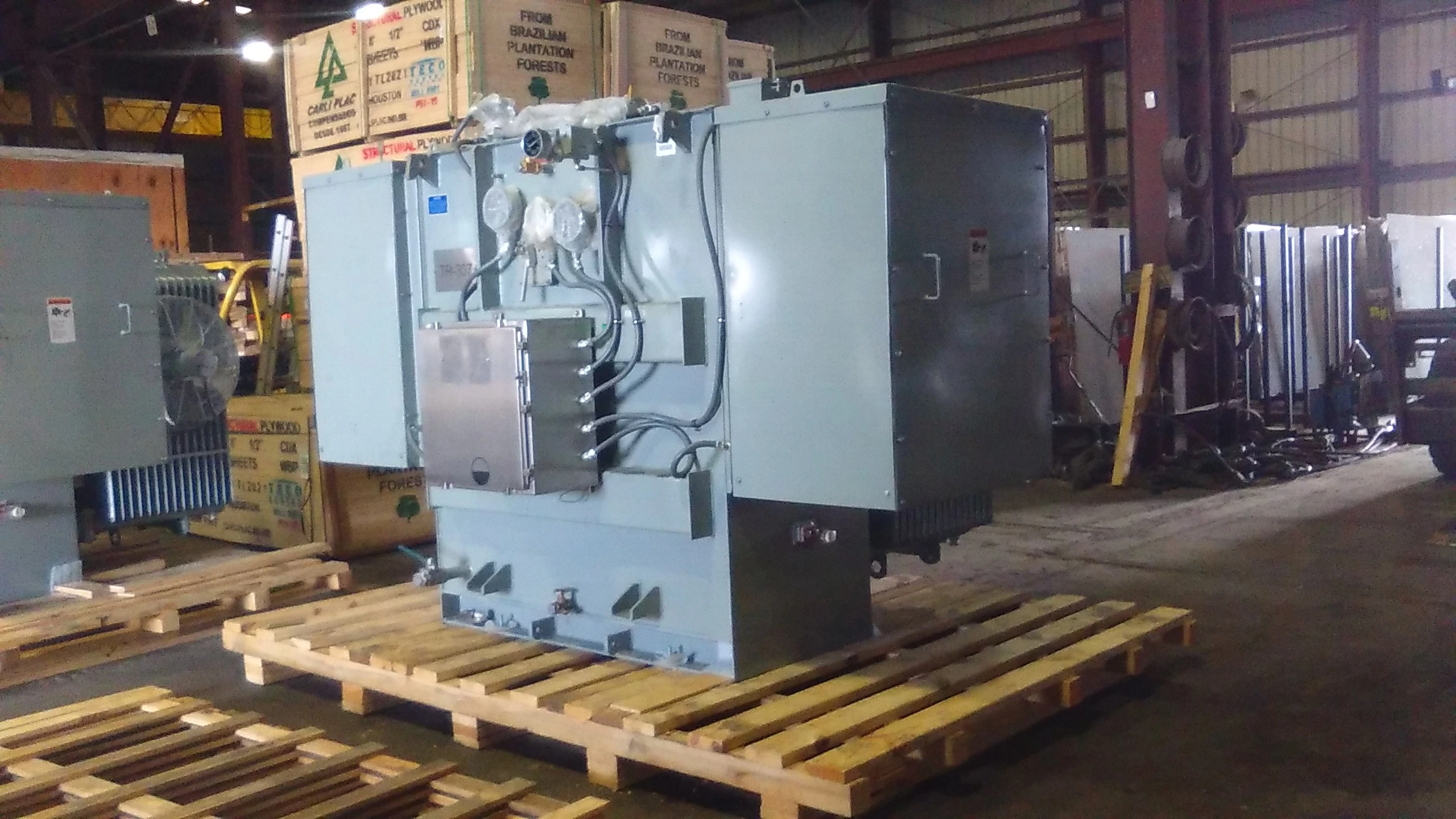
The 22 Stages of the Transformer Production Process:
Stage 1 – Approval on Technical Aspects Before Production
Challenge: Ensuring all technical aspects were reviewed and approved before production to avoid rework.
Management: Close coordination with the customer and GE factory to finalize specifications and prevent delays.
Stage 2 – RAAH/GE Technical Document Submittal to Customer for Approval
Challenge: Timely submission of comprehensive technical documentation to meet customer deadlines.
Management: Leveraged a streamlined review process, ensuring no document was delayed.
Stage 3 – Customer’s Technical Comments
Challenge: Gathering and addressing detailed feedback from the customer.
Management: Efficient collaboration with the customer to prioritize comments and swiftly integrate changes.
Stage 4 – RAAH/GE Technical Submittal to Customer Rev K02
Challenge: Ensuring all required technical revisions were incorporated into the documentation.
Management: Timely submission with accurate revisions to meet project milestones.
Stage 5 – Customer’s Technical Comments on Rev K02
Challenge: Handling potentially complex comments and revising technical documentation.
Management: Clear communication channels with the customer ensured quick resolution of technical concerns.
Stage 6 – GE Factory Review of Technical Comments to SALDOC-01-REV01
Challenge: Thorough internal review of customer comments to ensure all issues were addressed.
Management: GE’s engineering team conducted detailed reviews and provided prompt feedback.
Stage 7 – RAAH/GE Technical Submittal to Customer Rev K03
Challenge: Finalizing the revised submission with all technical adjustments.
Management: Precision and attention to detail were prioritized in preparing the final revision.
Stage 8 – Customer’s Technical Comments on Rev K03 & APPROVED
Challenge: Receiving and approving the final version of the technical documents.
Management: Swift review and approval by the customer ensured smooth progression to production.
Stage 9 – Technical Confirmation to GE Factory as per K03 Technical
Challenge: Aligning the factory’s production with the customer-approved technical documentation.
Management: Ensured alignment between the factory and the technical team for seamless production.
Stage 10 – GE Transformer Design/Drawing Progress and Submittal Plan
Challenge: Coordinating design and drawing submissions to meet customer deadlines.
Management: Regular updates and clear communication kept the design process on track.
Stage 11 – Record Drawing Submittal to Customer for Approval
Challenge: Preparing accurate record drawings for customer approval.
Management: Used dedicated teams to ensure that record drawings met quality and precision standards.
Stage 12 – HV / LV Windings and Core Preparation
Challenge: Ensuring precise winding and core preparations for optimal transformer performance.
Management: Tight quality control processes and expert oversight ensured consistency and quality.
Stage 13 – Bushing / Radiators Manufacturing
Challenge: Ensuring timely manufacturing of bushings and radiators to specification.
Management: Closely monitored manufacturing schedules to prevent delays in component availability.
Stage 14 – Control Panel and Enclosure
Challenge: Coordinating the production of control panels and enclosures within project timelines.
Management: Effective project planning ensured that the control panels and enclosures were built to specification and on schedule.
Stage 15 – Tap Changer and Accessories
Challenge: Ensuring precise tap changer installation with all necessary accessories.
Management: A detailed checklist ensured all accessories were included and the tap changers were properly installed.
Stage 16 – Pre-Assembly & Pressing
Challenge: Managing the critical pre-assembly and pressing stages to ensure all parts fit accurately.
Management: Rigorous checks during the assembly process minimized errors and avoided costly adjustments later.
Stage 17 – Painting
Challenge: Ensuring that the painting process met both aesthetic and protective standards.
Management: A dedicated team managed the painting process, ensuring uniformity and compliance with industry standards.
Stage 18 – Final Assembly
Challenge: Coordinating the final assembly of all transformer components.
Management: An efficient assembly line process ensured that the final assembly was completed without delays.
Stage 19 – Testing
Challenge: Testing the transformers to ensure they met all performance specifications.
Management: Thorough and rigorous testing processes were conducted to guarantee quality and safety.
Stage 20 – Testing Report/Photos Submission
Challenge: Timely submission of comprehensive testing reports and photos for customer review.
Management: Clear documentation and organized submission ensured all test results were communicated effectively.
Stage 21 – GE Complete Quality Conformance & Acknowledgment Report
Challenge: Ensuring all quality standards were met and documented.
Management: GE’s quality team performed detailed inspections, ensuring full compliance with international standards.
Stage 22 – Packing & Delivery
Challenge: Safe and efficient packing and transportation of the transformers.
Management: The final transformers were carefully packed to prevent damage during transport, and delivery was coordinated to ensure timely arrival at the site.
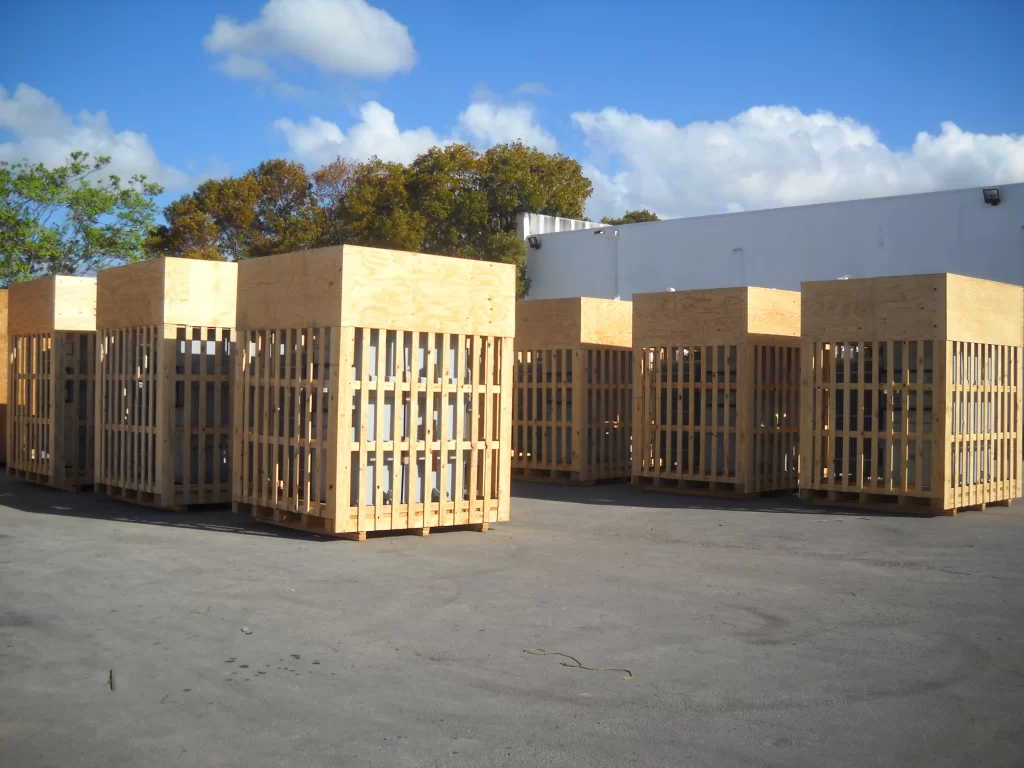
Conclusion:
Managing these 22 stages from technical approval to packing and delivery was a challenging yet well-coordinated process. Through meticulous planning, close collaboration with GE Prolec, and constant communication with the customer, the Bibiyana Gas Plant project team successfully navigated each stage to ensure the power transformers were delivered on time and to specification, enabling the plant to support the increased load from the BYO project and enhance its condensate recovery and gas production capabilities.
Get in touch at sales@raahgroup.com